
|
PRODUCTS : |
Products, Technologies, Services and Turnkey activities for Engineering Industries offered by Combustion & Heat Transfer Engineering Co.
are:
a. |
Detailed Engineering (on the basis of customer's / collaborator's / consultant's basic engineering) of most of the technological plants & machinery as well as utilities. |
b. |
Turnkey jobs, including system design, for fuel oil / tar installations, gas mains, burner front pipe work train for any fired equipments like furnaces, boilers, kilns, BF stoves, combustion system & metalling pre heater for hot air (900°C) blast for mini blast furnaces, etc., complete ladle heaters, tundish heaters, combustion system for hot mixer, drier for moist granulated slag, lime calcination plant, dolomite sintering plant, waste heat recovery systems, combustion & control systems. |
c. |
Design, manufacture, supply & installation, if required, of unfired pressure vessels, Combustion System (burners), recuperators, fired heaters, preheaters, super heaters, heat exchangers, etc. |
d. |
Technological fabrication & erection of carbon steel & alloy steel materials. |
e. |
Detailed engineering, inspection, refractory laying and / or refractory dry out & preheating of any large refractory installations. |
1. |
Liquid fuel installations
Storage tanks, out flow suction heaters, strainers, mat heaters, line
heaters, phs. Petroleum act, explosives formalities. |
2. |
All kinds of burners |
3. |
Hot air generators ( direct fired & indirect fired ) |
4. |
Ladle heaters / tundish nozzle preheater stand, scrap preheater,
anode furnace heating system, launders heating system |
5. |
Pressure vessels |
6. |
|
7. |
Ovens, driers |
8. |
Edible oil tank farms |
9. |
Recuperators |
10. |
Pipe spools, pipelines, ducts |
11. |
Dampers |
12. |
Furnaces & kilns, rotary kiln |
13. |
Torpedo ladle heating system |
14 |
Stacks |
15 |
Fired heaters, start-up air heaters, super heaters |
16 |
Engineering services |
-
Detail engineering & technological fabrication
Refractory design / detail engineering / supply / erection /
dry out & preheating
Consultancy in the area of air & water pollution
Consultancy in area of energy management boiler and other related areas

|
SERVICES : |
1. |
Refractory Dry Out Services : |
Refractory dry out services is available through Hotwork's U.K
Licensee
-
Hotwork is the pioneer of the convective heating process, which simplifies refractory dry-outs and heat-ups. The one-sided drying of monolithic refractories is an extremely complex transient heat and mass transfer phenomenon which includes chemical reactions throughout the
dry out. Moisture trapped in a refractory lining after a furnace or vessel rebuild is especially detrimental to optimum refractory performance. Network's convective heating method utilizes rapid heat transfer at all temperature levels. Our patented burners produce high velocity combustion, which is accurately controlled from ambient to temperatures in excess of 2500°F (1370°C). This high discharge rate circulates the products of combustion evenly throughout the vessel, regardless of size and configuration, producing overall temperature uniformity. The process results in fast, even moisture removal across the entire refractory lining allowing rapid furnace startups.
Hotwork has successfully completed dry-outs and heat-ups on:
Rotary Kilns Fluidized Beds Raw Mills
Alumina Calciners Coolers Mills
Vertical Kilns Calciners Coal Finish Mills
Hot work has been tremendously popular in the field of "REFRACTORY DRY OUT" and has numerous equipment to match its work endlessly. We have a special designed set of "HIGH VELOCITY BURNER" to completely remove moisture during the dry out process.
-
Furnace Heat up
Traditionally, small to medium-sized glass furnaces in the Asia Pacific region
have been heated-up in 7 (or more) days. This has become widely accepted as the “norm”, and it is perceived that a faster heat-up will result in an abbreviation of the eventual furnace campaign life.
This is a misconception. There is no technical reason why the refractories generally used in container and lighting glass furnace construction can not be heated up more rapidly. The only inhibiting factor is being able to adjust for, and control, furnace expansion.
(Exceptions would be where Dense Chrome blocks and “M” (fused alumina) Crowns are present.) By using the High Velocity burner system, there is no need for such a cautious approach. Your furnace can be safely heated-up from ambient to 1100/1200oC over a 3 or (maximum) 4 day period. This provides a substantial saving to you in terms of furnace downtime.
Over 100 furnaces have been heated-up in India & Abroad over the past 12 years, by (briefly) commencing combustion air reversals from the beginning of the heat-up, thereby pressurizing the furnace and optimizing temperature uniformity throughout, and using High Velocity burners to heat-up in 3 or 4 days (depending generally on the furnace size).
The results show no measurable difference in subsequent furnace campaign life versus furnaces which have been heated up over a schedule twice as long. WHY HAVE YOUR FURNACE SITTING IDLE FOR 3-4 DAYS LONGER THAN NECESSARY ?
2. |
Furnace Emergency Services : |
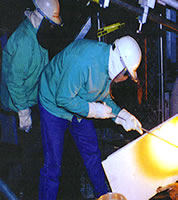
|
Hot work's unique
draining service allows draining rates up to 40
tons per hour per tap. Furnaces at or below grade
can be quickly drained using our high-pressure
water pumps, which allow a 2-meter lift, and pipe
runs in excess of 70 meters. |
|
Hot work offers
fast cullet filling systems capable of up to 60
tons per hour. We offer the original "dry"
filling equipment where air is used as the medium
for conveying the cullet out into the furnace
for quick melting and elimination of thermal shock
to the fill pockets plus systems to filter out
fines or wetting equipment to eliminate the dusting
of the superstructure. |
-
Sulfate Removal
:
Hot work uses special outlet nozzles in conjunction
with our unique Hotwork burners to quickly and safely
remove sulfates and borates from checker settings
to allow the furnace to operate at or near original
design parameters.
1. Block Checker Work
2. Sulfate Burning Away
3. Air Passage Ways Reestablished
3. |
Furnace Hot Repair Services : |
-
For Furnace Inspection
For Furnace Inspection & Ceramic Welding to enhance
the Life of Furnace with the international proven
technology.
-
Furnace Hot Repair
– With the guidance of Hot Repair Specialist
from abroad. Experience/ Specialization of SPECIALIST
is enclosed.
4. |
Details of Furnace Hot Repair Projects : |
• |
Emergency glass
leak repairs / prevention |
• |
Over coating melter sidewalls |
• |
Crown repairs to melter,
regenerator, ports, using hot insertion refractory
or casting. |
• |
Burner block replacement / Thermal couple block
replacement. |
• |
Tweel stone / crutch arch
replacement / canal assembly change - out. |
• |
Checker pack unplugging / checker change - out. |
• |
Water shut off gate fabrication / installation. |
• |
Furnace sealing after start-up. |
• |
Stopping breast wall roll-in. |
• |
Waist area - rebuilding stirrer grid, arch replacement. |
• |
Furnace construction & demolition. |
• |
Training of personal for day to day furnace preventive
maintenance. |
-
Regenerator Decongestion –
by using advance modern High Velocity Nurner System
with the best advance method.
Furnace Drilling/Tapping/Draining-
by using sophisticated light-weight Drilling Machine,
High Pressure Water Pump & appropriate drained
Glass Conveying System.
-
Furnace Control Cool Down- applying modem method
& Equipment.
-
Furnace Hot Repair- With the guidance of Hot Repair
Specialist from abroad.
Experience/Specialization of SPECIALIST is enclosed
-
Furnace Design / Supervision / Supply of Refractories
& other Furnace
equipments.
5. |
Furnace Design through Jack - Furnace design, New Zealand : |
Glass furnace & metallurgical furnace design are available through M/s Jack Furnace design.
The design includes |
- |
Furnace design |
|
- |
Furnace equipment design |
|
- |
Furnace Heat balance calculation |
|
- |
Design for furnace control along with instrumentation |
|
- |
Batch house design along with various equipments. |
|
- |
Design modification for existing Furnace. |
6. |
Torpedo ladle heating system : |
Torpedo ladle heating system are in operation with the appropriate specialized Combustion Equipment along with moveable trolley at various Steel Plants.
In addition we are executing Top Ignition Lance for Burning Trapped BF Gas for Steel Plant through TATA PROJECTS and TATA CONSULTANT.
We have developed Specialized Flare Stage Combustion System with Spark Igniter and Operation Through a Specialized PLC based Controller. |
|
|